Blog post -
The important path away from fossil plastics
Plastic is a great material. Perhaps that is the problem. Plastic works extremely well in an infinite variety of applications. Now we need to move to environmentally smart, fossil-free alternatives.
Plastic has many advantages – it is easy to produce, adapt and use. Since 1990, global production has more than tripled and in 2019, 368 million tonnes was produced. Already in 1989, plastics overtook steel production in terms of volume and are projected to reach 34 billion tonnes by 2050 (University of Georgia, 2017).
Yet, according to one estimate, 99 percent of all plastics are made from raw fossil materials. Greenpeace also estimates that 12 million tonnes of plastic end up in the oceans every year, and on top of that there is the growing problem of microplastics spreading in ecological systems.
Although plastics are difficult to replace, for example in some medical applications, it is clear that from an environmental perspective we need to reduce their use and bring the remaining plastics into a circular model.
EU Plastics Directive just the start
It may seem contradictory that we, as manufacturers of single-use products, wholeheartedly support the EU's Single-Use Plastics Directive (SUPD), which bans the use of single-use plastic products (see box below). Yet we do. It is something we feel strongly about.
“To reduce environmental and climate impact, we need to leave fossil resources where they belong – in the ground,” says Tomasz Doweyko, Marketing Director of the BioPak brand. “The EU and new laws will have a huge impact on our industry in the future. SUPD is just the start. So it is important for companies to actively keep up to date and to engage and communicate with their stakeholders.”
Systematic search for environmentally sound alternatives
An obvious follow-up question is, what are we doing to reduce our own use of virgin fossil plastics?
Even before SUPD, we had been phasing out fossil-based products from our range for several years, which is now being intensified with the new strategy.
“Our vision is to lead the industry towards circular solutions and net zero emissions and we want to be a positive role model”, says Tomasz. “We are working to reduce our use of plastics in general, with a particular focus on virgin fossil plastics. We have a zero vision for 2030 and we are currently mapping how much fossil plastic we have in our range. The aim is to replace it with paper and fiber
wherever possible. Here we have a great opportunity to grow. When we have to use plastic, for example in food contact, we should use bioplastics or recycled plastics.”
Several positive initiatives in 2021
Already in 2021, we introduced paper-based, fossil-free outer packaging for some products. In our own production we have replaced latex binders with fossil-free binders in table coverings and napkins. We have also replaced plastic cutlery with products made of wood and paper.
“In a broader perspective, sustainability is about looking ahead and seeing where we want to go, but also about maintaining quality of life and well-being in the short and long term. It links social and ecological sustainability. We want to do what we can to help people, both today and in the future, to meet and feel good around food and drink,” Tomasz concludes.
How the EU Plastics Directive affects us
The EU Single Use Plastics Directive (EU 2019/904) entered into force on July 3, 2021. This means that the BioPak and Duni business areas will no longer sell products made entirely or partly of plastic. This applies to: Cutlery / Plates / Straws / Stirrers BioPak and Duni products will also be labeled according to the new, harmonized rules also introduced for products that are partly made of plastic. Due to some ambiguities in the Directive, full implementation in EU Member States is delayed. Duni Group interprets the rules as meaning that the Directive currently only applies to products placed on the market after July 3, 2021.
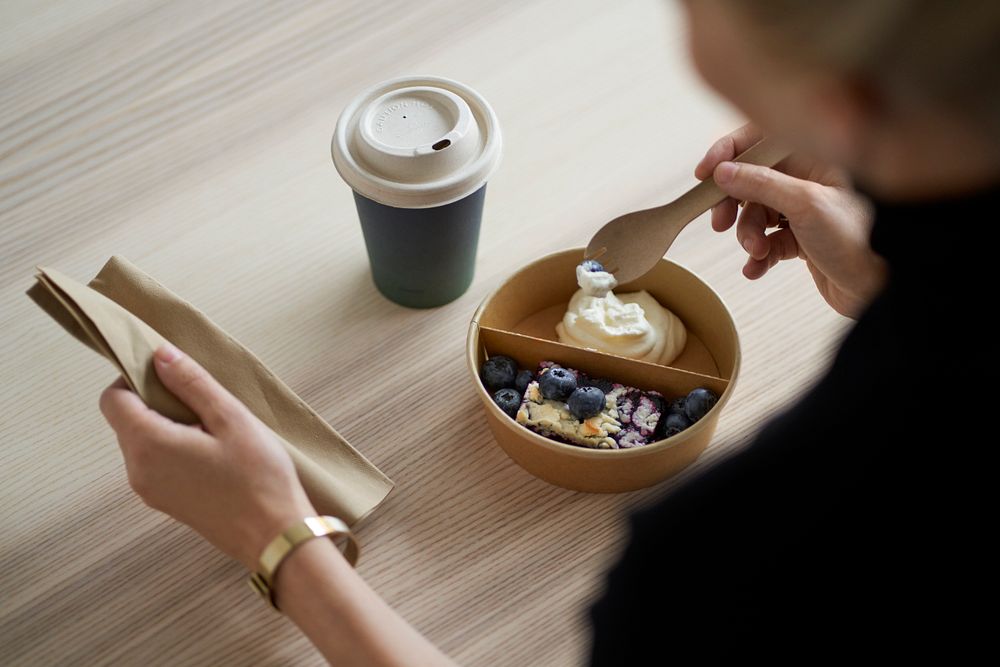
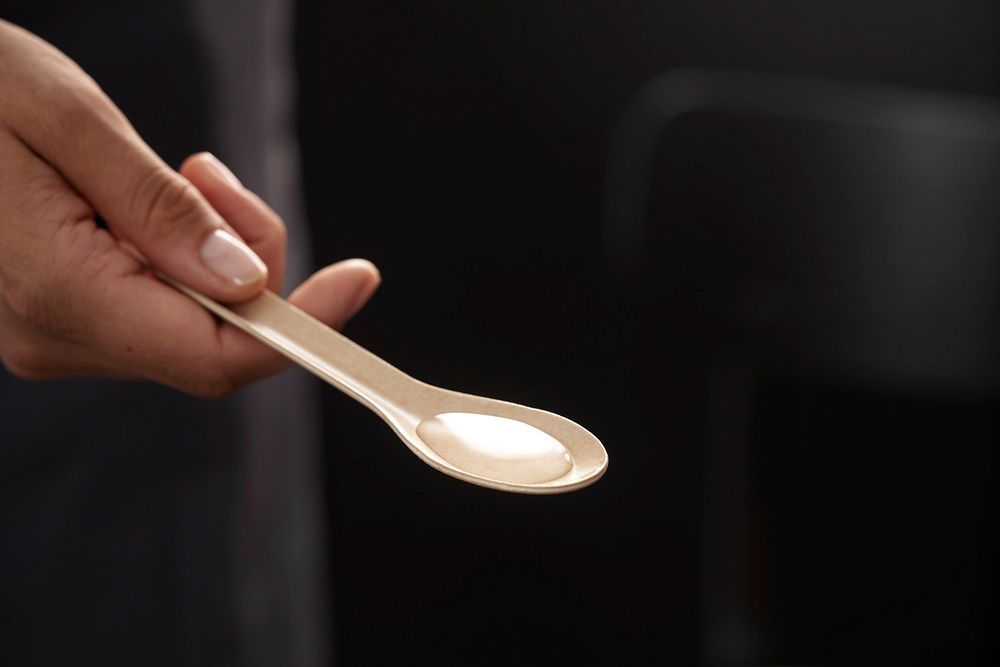